Ecofriendly Recycling of Lithium-Ion Batteries
Duesenfeld combines mechanical, thermodynamic and hydrometallurgical processes in a patented process. The process achieves the highest material recovery rates with low energy consumption. This is made possible by a process control with low temperatures, in which toxic hydrogen fluoride are not produced. Exhaust gas scrubbing is not necessary in the mechanical processing step. The fluorides are removed in a targeted and safe manner in hydrometallurgy.
Duesenfeld operates the only recycling process that, in addition to the usual metals, also supplies graphite, electrolytes and lithium for material recycling. Material recycling does not mean a declaration as a building material, e.g. for road construction, but all metals are recovered with high recovery rates in the form of high-quality secondary raw materials up to battery quality. The production of secondary raw materials with the Duesenfeld recycling process saves 8.1 tons of CO2 per ton of recycled batteries compared to the primary extraction of the raw materials3)4). Compared to conventional melting processes, the Duesenfeld process saves 4.8 tons of CO2 per ton of recycled batteries3)5), compared to mechanical processes with exhaust gas scrubbing, the saving is 1 ton of CO2 per ton of recycled battery3).
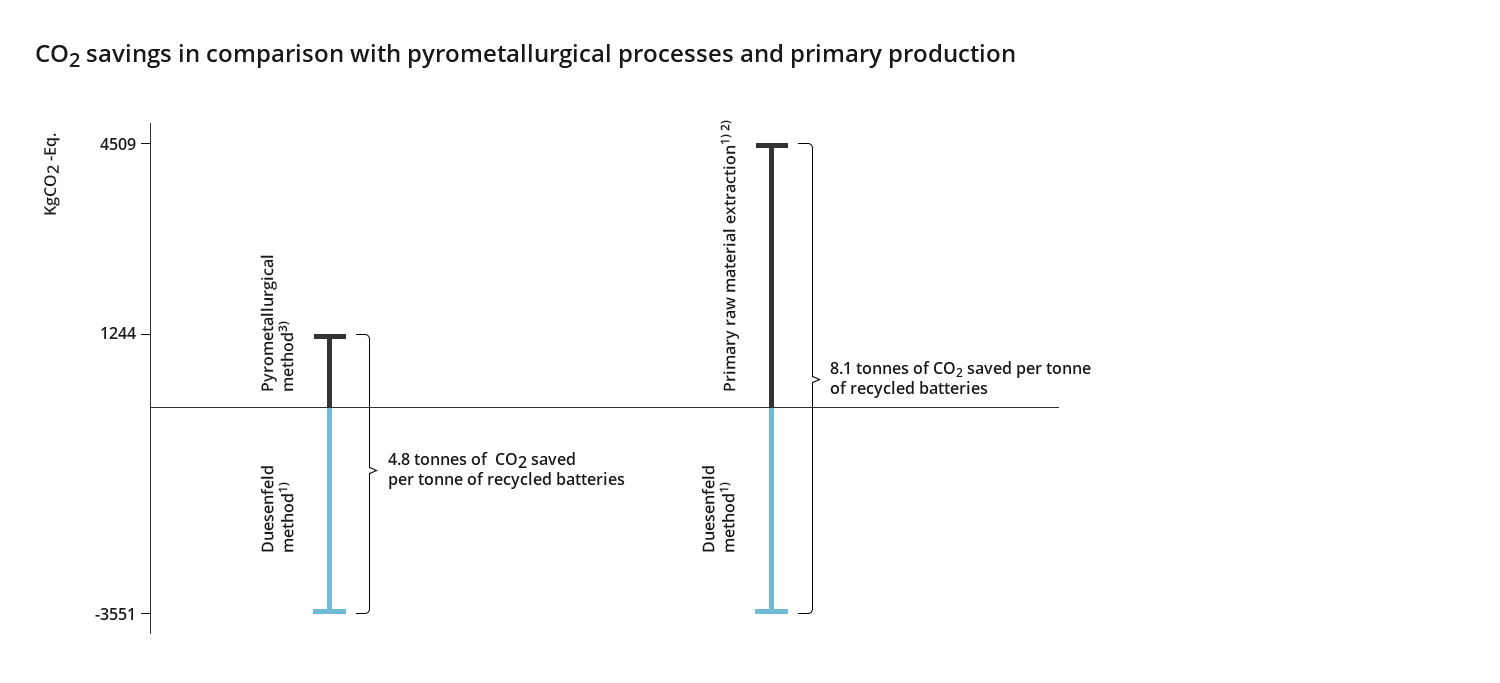
Electric mobility is Climate Friendly only with Duesenfeld Recycling
CO2 savings from electric mobility to slow down global warming must not be nullified by inappropriate recycling of the batteries. With the environmentally friendly process from Duesenfeld, no CO2 is produced during mechanical recycling, no toxic filter materials have to be deposited.
The Duesenfeld process achieves a more than twice as high material recovery rate for lithium-ion batteries as conventional recycling methods through mechanical processing. Supplemented by hydrometallurgical processes, almost complete recycling is possible. End-of-life batteries are usually classified as hazardous goods and transported in battery transport containers. The electrolyte is separated from the other substances by mechanical processing with modular recycling systems on site, the resulting products no longer require special hazardous goods transport containers. These intermediates are transported in standard containers, which makes it possible to transport 7 times the amount per truck. This reduction in the transport of dangerous goods saves a large part of the total recycling costs of the batteries.
Our focus is on recycling the batteries as completely as possible. Duesenfeld achieves a recycling rate of 72% in mechanical recycling, with the processing of the Duesenfeld Black®in Duesenfeld hydrometallurgy, the material recycling rate increases to 91%. Only the separator film and the high boiler portion of the electrolyte are not recovered at the moment. Duesenfeld thus goes far beyond the current requirements of the EU Battery Directive 2006/66/EC.