Umweltfreundliches Recycling von Lithium-Ionen-Batterien
Duesenfeld verbindet in einem patentierten Verfahren mechanische, thermodynamische und hydrometallurgische Prozesse. Das Verfahren erzielt bei geringem Energieaufwand höchste stoffliche Rückgewinnungsraten. Ermöglicht wird das durch eine Prozessführung mit niedrigen Temperaturen, bei der giftige Fluorwasserstoffe nicht entstehen. Eine Abgaswäsche ist im mechanischen Verarbeitungsschritt nicht notwendig. Die Fluoride werden gezielt und sicher in der Hydrometallurgie entfernt.
Duesenfeld betreibt den einzigen Recyclingprozess, der neben den üblichen Metallen auch den Graphit, den Elektrolyten und das Lithium einer stofflichen Verwertung zuführt. Stoffliche Verwertung heißt keine Deklarierung als Baustoff, z.B. für Straßenbau, sondern alle Metalle werden mit hohen Rückgewinnungsraten in Form hochwertiger Sekundärrohstoffe bis hin zu Batteriequalität zurückgewonnen. Die Produktion von Sekundärrohstoffen mit dem Duesenfeld Recyclingprozess spart 8,1 Tonnen CO2 pro Tonne recycelter Batterien im Vergleich zur Primärgewinnung der Rohstoffe ein3)4). Im Vergleich zu üblichen Einschmelzprozessen spart das Duesenfeld Verfahren 4,8 Tonnen CO2 pro Tonne recycelter Batterien ein3)5), im Vergleich zu mechanischen Verfahren mit Abgaswäsche beträgt die Einsparung 1 Tonne CO2 pro Tonne recycelter Batterien1).
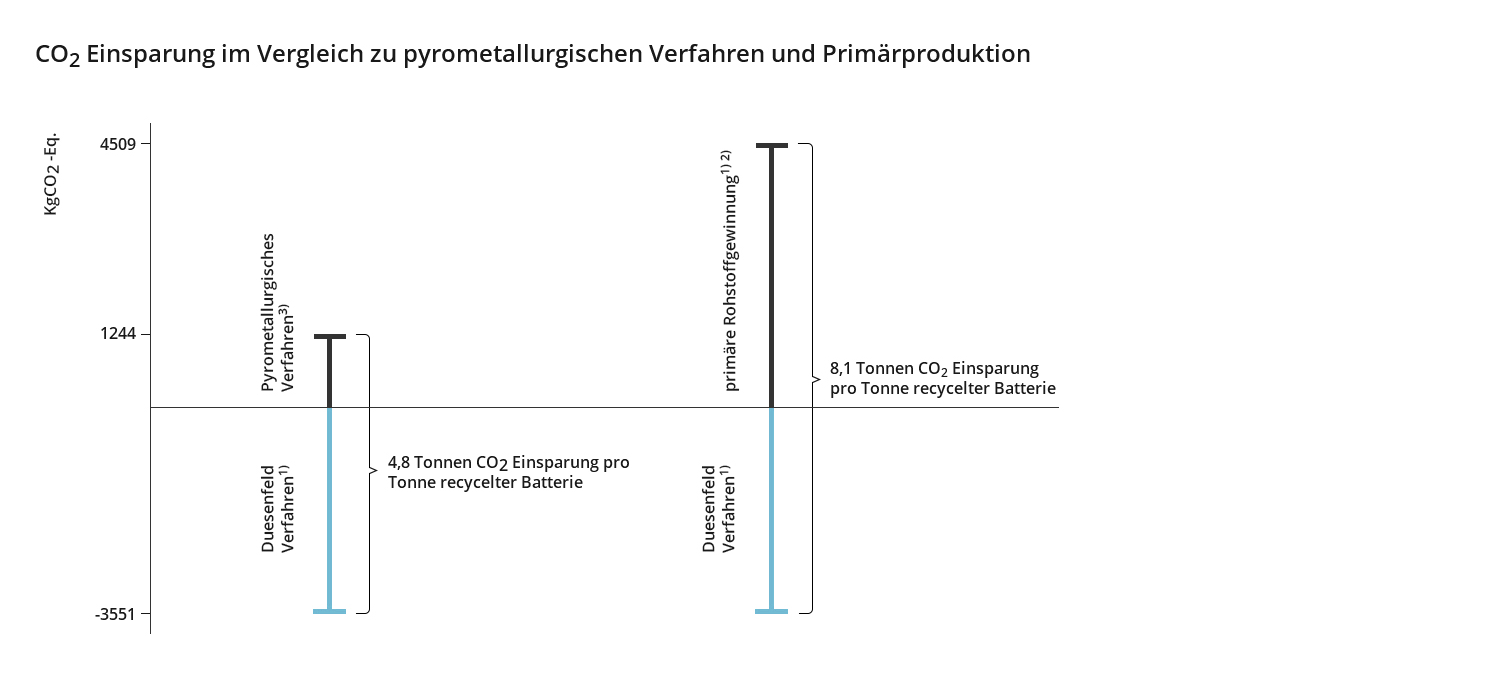
Elektromobilität ist nur mit dem Duesenfeld-Recycling klimafreundlich
CO2-Einsparungen der Elektromobilität zur Verlangsamung der Erderwärmung dürfen nicht durch ungeeignetes Recycling der Batterien zunichte gemacht werden. Mit dem umweltfreundlichen Verfahren von Duesenfeld entsteht kein CO2 beim mechanischen Recycling, es müssen keine giftigen Filterstoffe deponiert werden.
Das Duesenfeld Verfahren erzielt bei Lithium-Ionen-Batterien durch mechanische Aufbereitung eine mehr als doppelt so hohe stoffliche Rückgewinnungsrate als herkömmliche Recyclingmethoden. Ergänzt durch hydrometallurgische Prozesse ist ein nahezu vollständiges Recycling möglich. Üblicherweise werden End-of-life-Batterien als Gefahrgut eingestuft und in Batterietransportbehältern transportiert. Durch die mechanische Verarbeitung mit modular aufbaubaren Recyclinganlagen vor Ort wird der Elektrolyt von den übrigen Stoffen getrennt, die entstandenen Produkte benötigen keine speziellen Gefahrguttransportbehälter mehr. Diese Zwischenprodukte werden in Standardbehältnissen transportiert, wodurch pro LKW die 7-fache Menge transportiert werden kann. Durch diese Reduzierung der Gefahrguttransporte wird ein Großteil der gesamten Recyclingkosten der Batterien eingespart.
Unser Fokus liegt auf einer möglichst vollständigen stofflichen Verwertung der Batterien. Duesenfeld erreicht im mechanischen Recycling eine Recyclingquote von 72 %, mit der Aufbereitung der Duesenfeld Black® in der Duesenfeld Hydrometallurgie erhöht sich die stoffliche Recyclingquote auf 91 %. Lediglich die Separatorfolie und der Schwersiederanteil des Elektrolyten werden momentan nicht zurückgewonnen. Damit geht Duesenfeld weit über die derzeitigen Anforderungen der EU Batterierichtlinie 2006/66/EC hinaus.